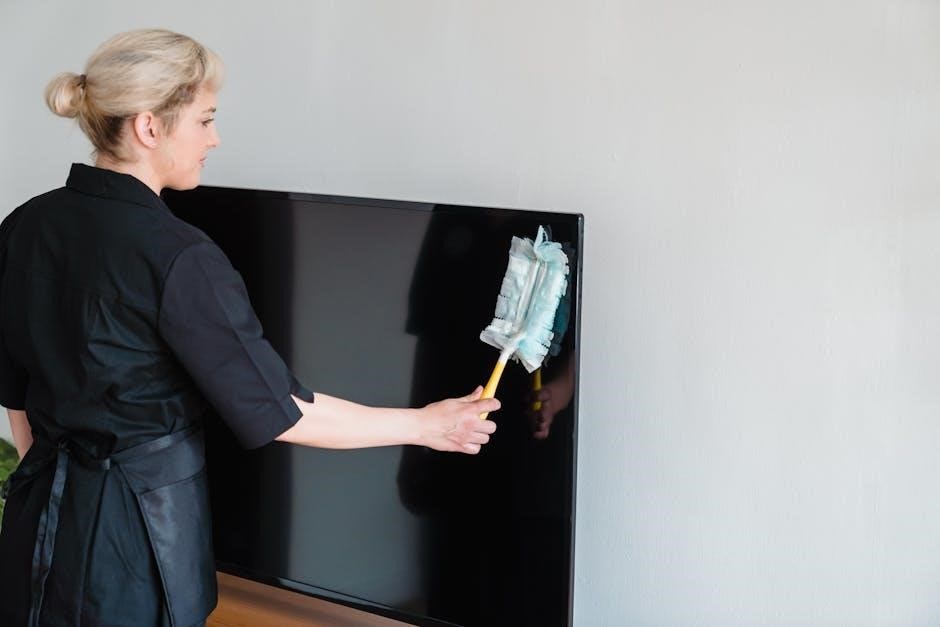
The Rexroth A10V Service Manual provides essential guidance for maintaining and repairing the A10V hydraulic pump, ensuring optimal performance and longevity. It covers key features, safety protocols, and technical specifications to help users understand and service the pump effectively.
1.1 Overview of the A10V Hydraulic Pump
The Rexroth A10V hydraulic pump is a high-performance, variable displacement pump designed for hydrostatic drives in open circuits. It features an axial piston rotary group in a swashplate design, enabling precise control over flow rates and pressure; The pump is widely used in industrial and mobile applications due to its efficiency, reliability, and adaptability to varying operational demands; With a robust construction and advanced hydraulic technology, the A10V ensures consistent performance under diverse conditions, making it a key component in modern hydraulic systems.
1.2 Importance of the Service Manual for Maintenance and Repair
The Rexroth A10V Service Manual is a crucial resource for ensuring the pump operates at peak efficiency. It provides detailed instructions for routine maintenance, troubleshooting, and repair, helping users identify and address potential issues before they escalate. The manual includes safety guidelines, technical specifications, and step-by-step procedures, making it indispensable for technicians and operators. By following the manual’s recommendations, users can extend the pump’s service life, minimize downtime, and maintain system performance. Proper use of the manual ensures compliance with manufacturer standards and supports overall system reliability.
Key Features of the Rexroth A10V Hydraulic Pump
The A10V pump features variable displacement, axial piston rotary group, and swashplate design, enabling precise flow control in hydrostatic drives and open circuits for optimal performance.
2.1 Variable Displacement Pump Design
The A10V’s variable displacement design allows for adjustable flow rates, controlled by the swashplate angle, ensuring efficient operation across varying load conditions. This feature enables precise pressure and flow management, optimizing system performance while minimizing energy consumption. The pump’s ability to vary displacement makes it highly adaptable for different applications, from low-speed, high-torque scenarios to high-speed, low-torque operations, providing flexibility and reliability in hydrostatic drives and open circuits.
2.2 Axial Piston Rotary Group in Swashplate Design
The A10V features an axial piston rotary group integrated with a swashplate design, enabling smooth and efficient operation. The swashplate controls the piston’s stroke, allowing for variable displacement and precise flow control. This design enhances the pump’s ability to handle high pressures and flow rates while maintaining compactness and durability. The axial pistons and swashplate work in harmony to provide consistent performance, making the A10V ideal for hydrostatic drives and open circuit applications, ensuring reliability and versatility in various industrial settings.
2.3 Application in Hydrostatic Drives and Open Circuits
The A10V pump is specifically designed for use in hydrostatic drives and open circuits, offering precise control over fluid flow and pressure. Its variable displacement design makes it ideal for applications requiring adjustable output, ensuring efficient operation across varying loads. The pump’s swashplate technology allows for smooth transition between different operational modes, making it suitable for both low-speed, high-torque scenarios and high-speed applications. This versatility ensures reliable performance in industrial machinery, mobile equipment, and other systems requiring consistent hydraulic power delivery.
Safety Guidelines for Handling the A10V Pump
Always wear personal protective equipment, including safety glasses and gloves, when handling the A10V pump. Be aware of potential hazards like high pressure and moving components.
3.1 Personal Protective Equipment Requirements
When handling the A10V pump, wear safety glasses, gloves, and steel-toe boots to protect against hydraulic fluid splashes and moving parts. Coveralls are recommended to prevent skin contact with hazardous materials. Ensure proper ventilation in the work area to avoid inhalation of fumes. Avoid loose clothing that could get caught in machinery. Always follow the manual’s safety guidelines to minimize risks during maintenance and repair. Proper PPE is crucial for preventing injuries and ensuring a safe working environment.
3.2 Hazards Associated with Hydraulic Systems
Hydraulic systems pose risks such as high-pressure fluid injection, which can cause severe injury. Sudden component failure or fluid leakage under pressure can lead to accidents. Electrical components in the A10V pump are sensitive to moisture, and improper use in wet conditions can cause malfunctions. Additionally, exposure to hydraulic fluids can be harmful, requiring proper handling and disposal. Always ensure the system is de-energized before maintenance to prevent unexpected startup. Adhering to safety guidelines and using appropriate protective equipment minimizes these risks, ensuring a safer working environment when servicing the A10V pump.
3.3 Proper Use and Avoidance of Improper Applications
Proper use of the A10V pump ensures safe and efficient operation. Avoid exceeding specified pressure and flow limits to prevent damage. Misuse, such as operating in environments with extreme temperatures or contaminants, can lead to premature wear. Always adhere to the guidelines outlined in the service manual for installation, maintenance, and repair. Improper applications, like using the pump in closed-loop systems without proper configuration, can cause malfunctions. Ensure all electrical components are protected from moisture and that hydraulic fluids are handled correctly. Following these guidelines minimizes risks and extends the pump’s service life.
Technical Specifications of the A10V Pump
The A10V pump features variable displacement, axial piston design, and swashplate technology. It operates within specific flow rates, pressure limits, viscosity ranges, and temperature thresholds for optimal performance.
4.1 Flow Rates and Pressure Limits
The Rexroth A10V pump is designed to deliver variable flow rates, proportional to the drive speed, ensuring efficient operation across diverse applications. Pressure limits are clearly defined to prevent system overload, with maximum ratings specified to maintain performance and longevity. Exceeding these limits can lead to premature wear or failure. The pump’s swashplate design allows for precise control of flow and pressure, enabling smooth operation in hydrostatic drives and open circuits. Adhering to these specifications is crucial for optimal functionality and safety. Always consult the manual for detailed charts and guidelines tailored to specific operating conditions.
4.2 Viscosity and Temperature Ranges
The Rexroth A10V pump operates efficiently within specific viscosity and temperature ranges to ensure optimal performance. The recommended viscosity range for hydraulic fluids is typically between 10 to 400 mm²/s, depending on operating conditions. Temperature limits are specified to prevent fluid degradation and maintain system integrity, with maximum operating temperatures generally not exceeding 100°C. Proper fluid selection and temperature monitoring are critical to avoid premature wear and ensure reliable operation. Always refer to the manual for detailed guidelines on fluid compatibility and temperature control to maximize pump longevity and efficiency.
4.3 Compatibility with Hydraulic Fluids
The Rexroth A10V pump is designed to operate with specific hydraulic fluids to ensure optimal performance and longevity. It is essential to use fluids that meet the manufacturer’s specifications, typically mineral-based oils with adequate viscosity and lubricity properties. Incompatible fluids can lead to premature wear, corrosion, or system failure. Always avoid using fluids with contaminants or additives that may degrade pump components. Proper fluid selection and maintenance are critical to uphold the pump’s efficiency and service life. Refer to the manual for a detailed list of approved fluids and guidelines for safe operation. Improper fluid use may void warranty terms.
Installation and Commissioning
Installation involves proper mounting, connection, and alignment. Commissioning requires start-up procedures, system testing, and performance verification, ensuring safe and efficient operation as per manual guidelines.
5.1 Pre-Installation Checks and Preparation
Before installing the A10V pump, ensure all components are inspected for damage. Verify compatibility with hydraulic fluids and system specifications. Clean the area to prevent contamination. Check that all electrical connectors are secure and meet manual standards. Properly prepare mounting surfaces and ensure alignment tools are ready. Review safety guidelines and wear protective equipment. Confirm that all necessary tools and spare parts are available. Follow the manual’s step-by-step instructions to prevent errors during installation. Proper preparation ensures a smooth and safe commissioning process, minimizing potential issues and ensuring optimal performance.
5.2 Mounting and Alignment Procedures
Mounting the A10V pump requires precise alignment to ensure proper operation and prevent wear. Secure the pump to a stable base using recommended fasteners. Use alignment tools to ensure the pump’s drive shaft is correctly positioned with the motor or engine. Check for any play or misalignment, which can lead to vibration and noise. Tighten all bolts gradually to avoid uneven stress. Refer to the manual for torque specifications and alignment tolerances. Proper mounting and alignment are critical for maintaining efficiency, reducing vibration, and extending the pump’s service life. Ensure all connections are secure before starting the system.
5.3 Initial Start-Up and Testing
Before start-up, ensure all connections are secure and the system is properly primed. Check hydraulic fluid levels and filter cleanliness. Start the pump at low pressure to avoid sudden surges. Monitor flow rates and pressure readings to confirm they match specifications. Listen for unusual noises or vibrations, which may indicate misalignment or improper installation. Test the pump under varying loads to ensure consistent performance; Inspect for leaks around seals and connections. Document all findings and adjust settings as needed. Proper initial testing ensures reliable operation and helps identify potential issues early, preventing costly downtime and extending equipment life.
Maintenance and Service Intervals
Regular maintenance ensures optimal performance and extends the A10V pump’s service life. Schedule routine inspections, lubrication, and wear part replacements as outlined in the manual.
6.1 Routine Inspection and Lubrication
Regular inspections are crucial for identifying wear and ensuring smooth operation. Check for signs of leakage, worn seals, or damaged components. Lubrication is essential to reduce friction and prevent overheating. Use high-quality hydraulic fluids compatible with the A10V pump, adhering to viscosity and temperature guidelines. Refer to the manual for recommended lubrication intervals and procedures. Always wear safety gear, including gloves and eye protection, during maintenance. Proper lubrication and timely inspections help extend the pump’s lifespan and maintain efficiency. Follow the service manual’s guidelines to ensure optimal performance and safety.
6.2 Replacement of Wear Parts and Seals
Replacement of wear parts and seals is critical to maintaining the A10V pump’s performance and preventing fluid leakage; Always use genuine Bosch Rexroth parts to ensure compatibility and reliability. Begin by disconnecting the hydraulic lines and draining the system. Remove the worn components, such as piston shoes or valve plates, and inspect for additional damage. Clean the areas thoroughly before installing new seals or parts. Apply a thin layer of hydraulic fluid to seals for proper seating. Reassemble the pump carefully, ensuring all connections are secure and torque specifications are met. Test the system under low pressure to confirm integrity before full operation.
6.3 Bearing Service Life and Replacement
The service life of bearings in the A10V pump is influenced by operating conditions, load, and lubrication quality. Regular inspection is essential to identify wear early. When replacing bearings, ensure all mating surfaces are clean and free from contamination. Use specialized tools to avoid damage during disassembly and reassembly. Apply the recommended lubrication to the new bearings before installation. Tighten bolts to the specified torque values to prevent premature wear or failure. After replacement, perform a test run at reduced load to verify proper operation and alignment. Consult the manual for specific torque specifications and procedures to ensure reliability and longevity of the pump.
Troubleshooting Common Issues
The manual assists in diagnosing issues like pressure fluctuations, noise, or leaks, providing step-by-step solutions to restore optimal pump performance and minimize downtime.
7.1 Identifying and Diagnosing Faults
The Rexroth A10V service manual guides users in identifying faults through systematic checks. Common issues include abnormal noise, vibration, or pressure fluctuations. Troubleshooting begins with visual inspections for wear or damage. Users should monitor system parameters and compare them to specifications. Listening for unusual sounds or observing performance deviations helps pinpoint problems. The manual provides charts and symptom-based guides to diagnose root causes, such as faulty valves or improper settings. It also advises on referencing error codes and performing functional tests to confirm issues before proceeding with repairs.
7.2 Resolving Pressure and Flow Irregularities
Addressing pressure and flow irregularities in the A10V pump involves checking system settings and fluid conditions. The manual recommends verifying pump controls and pressure relief valves for proper adjustment. Ensure hydraulic fluid viscosity aligns with operating temperatures to maintain optimal flow. Inspect suction lines for blockages and ensure the reservoir level is adequate. Testing pressure sensors and comparing readings with expected values helps identify malfunctions. Adjusting the pump’s displacement or replacing faulty components, such as worn piston shoes, can restore normal operation. Always refer to the manual’s troubleshooting charts for specific guidance on resolving these issues efficiently.
7.3 Addressing Noise and Vibration Problems
Noise and vibration issues in the A10V pump often stem from improper installation, misalignment, or worn components. The manual advises inspecting the pump’s mounting, ensuring proper alignment with the drive system, and checking for loose connections. Worn bearings, shafts, or piston shoes can cause vibration and should be replaced. Additionally, imbalanced rotating parts or incorrect fluid levels may contribute to noise. Regular lubrication and adherence to maintenance schedules can prevent these issues. Always consult the manual’s troubleshooting charts for specific diagnostics and solutions to restore smooth operation and minimize wear on critical components.
Repair and Overhaul Procedures
Repair and overhauling the A10V pump involves disassembly, inspection, and replacement of worn parts. Ensure proper tools and adherence to manual guidelines for successful reassembly and testing.
8.1 Disassembly and Inspection Steps
Disassembling the A10V pump requires careful preparation and specialized tools. Begin by draining hydraulic fluid and disconnecting electrical components. Remove external fittings and bolts, then separate major components like the swashplate and piston assembly. Inspect each part for wear, damage, or contamination. Use calibrated tools to measure clearances and check for alignment issues. Document all findings to guide repairs. Ensure a clean, organized workspace to prevent losing or damaging small parts. Refer to the manual for specific torque values and reassembly sequences to maintain pump integrity and performance.
8.2 Reassembly and Testing Post-Repair
Reassembly of the A10V pump must follow the manual’s torque specifications and alignment guidelines to ensure proper function. Start by installing the piston assembly and swashplate, ensuring correct orientation. Reattach the valve plate and port cover, verifying all connections are secure. Reconnect electrical sensors and test their functionality. Prime the pump before initial start-up to prevent dry running. Perform a leakage test and check for unusual noise or vibration. Record performance metrics to confirm compliance with factory standards. If issues arise, revisit the repair steps or consult the manual for troubleshooting guidance. Proper testing ensures reliable operation post-repair.
8.3 Tools and Equipment Required for Overhaul
Overhauling the A10V pump requires specialized tools, including a torque wrench for precise bolt tightening, a micrometer for measuring parts, and a hydraulic test bench to verify performance. Essential tools also include socket sets, pliers, and seal installation kits. A clean, well-lit workspace is crucial to prevent contamination. Proper lifting equipment may be needed for heavy components. Always reference the service manual for specific tool recommendations and safety guidelines. Using genuine Bosch Rexroth tools ensures compatibility and reliability during the overhaul process. Adhere to manufacturer guidelines to maintain warranty validity and operational safety.
Electrical Components and Sensors
The A10V pump integrates advanced electrical components, including sensors for pressure, flow, and temperature monitoring. These components ensure precise control and communication within hydraulic systems, enhancing operational efficiency and safety.
9.1 Integration of Electronic Controls
The Rexroth A10V pump features advanced electronic controls that seamlessly integrate with its hydraulic systems. These controls enable precise monitoring and adjustment of pump performance through embedded sensors. By interfacing with external systems, they ensure real-time data exchange for efficient operation. The electronic controls also support diagnostic capabilities, allowing for quick identification and resolution of issues. This integration enhances the pump’s adaptability to varying operational demands and ensures reliable performance in diverse applications. Regular updates and compatibility with modern control systems further underscore the importance of electronic controls in maintaining optimal functionality.
9.2 Calibration and Adjustment of Controllers
Calibration and adjustment of controllers for the Rexroth A10V pump are critical for ensuring precise operation and optimal performance. The service manual provides detailed steps for calibrating electronic controllers, emphasizing the use of specialized tools and software. Proper alignment with system requirements is essential to maintain accuracy. Regular adjustments may be necessary to account for wear or operational changes. Improper calibration can lead to inefficiency or system malfunctions, making adherence to the manual’s guidelines crucial. Controllers must also be integrated with sensors for real-time feedback, ensuring seamless communication and reliable functionality.
9.3 Protection of Electrical Components from Moisture
Protecting electrical components from moisture is vital to ensure the reliability and longevity of the Rexroth A10V pump. The service manual emphasizes the importance of preventing water exposure, as it can lead to corrosion, short circuits, and system failure. Proper sealing and insulation of electrical parts are essential. Additionally, the manual recommends using protective coatings and installing components in dry environments. Regular inspections should be conducted to detect any signs of moisture ingress. Adhering to these guidelines ensures optimal performance and prevents costly repairs due to water-related damage. Proper maintenance is key to safeguarding the pump’s electrical systems.
Environmental and Operational Considerations
Environmental considerations include proper disposal of hydraulic fluids and adherence to regulations. Operational factors involve managing extreme temperatures and contamination to ensure efficient, eco-friendly performance of the A10V pump.
10.1 Operating in Extreme Conditions
Operating the A10V pump in extreme conditions requires careful consideration of temperature, humidity, and contamination. High or low temperatures can affect hydraulic fluid viscosity, potentially leading to performance issues. Ensure the pump is protected from moisture and debris to maintain efficiency. Extreme conditions may necessitate specialized fluids or additional protective measures. Always refer to the service manual for guidelines on operating in harsh environments to prevent damage and ensure reliable performance. Proper preparation and maintenance are crucial for sustained functionality in challenging operational settings.
10.2 Compliance with Environmental Regulations
Compliance with environmental regulations is crucial when operating and maintaining the A10V hydraulic pump. Proper disposal of hydraulic fluids and contaminated materials must adhere to local and international environmental laws. The service manual emphasizes the importance of using biodegradable fluids where possible to minimize ecological impact. Additionally, electrical components and sensors must be protected from moisture to prevent contamination. Users are advised to consult regional environmental agencies for specific guidelines. By following these practices, operators can ensure sustainable and responsible use of the A10V pump, aligning with global environmental standards.
10.3 Proper Disposal of Used Hydraulic Fluids
Proper disposal of used hydraulic fluids from the A10V pump is essential to prevent environmental contamination. The service manual strongly advises against draining fluids into sewers or waterways. Instead, fluids should be collected in appropriately labeled, leak-proof containers and taken to authorized disposal facilities. Users must adhere to local and national environmental regulations to ensure safe and responsible disposal. Improper disposal can lead to severe ecological damage and legal consequences. Always consult local environmental authorities for specific guidelines and ensure compliance with all applicable laws to protect the environment.
Warranty and Support Information
The A10V service manual outlines warranty terms, support contacts, and spare part availability, ensuring comprehensive assistance for users maintaining their hydraulic pumps efficiently.
11.1 Warranty Coverage and Terms
The Rexroth A10V service manual details warranty coverage, specifying the duration and conditions under which repairs or replacements are covered. It outlines the scope of warranty, including parts and labor, and highlights exclusions such as misuse or improper maintenance. Users must adhere to specified service intervals and guidelines to maintain warranty validity. The manual also provides procedures for submitting warranty claims and emphasizes the importance of proper documentation. Understanding these terms ensures compliance and maximizes protection for the hydraulic pump, offering peace of mind for operators and maintainers.
11.2 Contacting Bosch Rexroth Support
For assistance with the A10V hydraulic pump, users can contact Bosch Rexroth support through various channels. The service manual provides detailed contact information, including website links, phone numbers, and email addresses. Customers are encouraged to reach out for technical inquiries, spare parts, or repair services. Local distributors and service centers are also available to provide regional support. When contacting support, having the pump’s serial number and specific details about the issue ensures quicker resolution. Bosch Rexroth’s global network ensures prompt and reliable assistance, maintaining operational efficiency and minimizing downtime for users worldwide.
11.3 Availability of Spare Parts and Service Centers
Bosch Rexroth maintains an extensive network of service centers and distributors worldwide, ensuring easy access to genuine spare parts for the A10V pump. Users can locate their nearest service center through the official website or by contacting local distributors. Genuine parts are critical for maintaining performance and safety, and Bosch Rexroth guarantees their quality and compatibility. Additionally, the company offers online resources to help customers identify and order the correct spare parts efficiently. This global support infrastructure ensures minimal downtime and maximizes operational reliability for A10V pump users across industries.